3D金属造形サービスのご紹介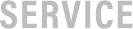
3D金属造形サービスについて
伊福精密では3D金属プリンターまたは樹脂3Dプリンターを用いた3D金属造形サービスを提供しております。 お客様から図面(3Dモデル)を送っていただき、その3Dデータから金属材料、もしくは樹脂材料にて3D造形プリントするサービスです。
3D造形プリント後の造形物は、三次元測定器(非接触光学式3次元デジタイザ) Carl Zeiss CONTURA-HTGを用いて、スキャニングさせて頂き、精密な品質測定をさせていただきます。3D金属プリンターは製品開発にて、試作品を金型レスで最終製品を製造できる為、大幅なコスト削減、納期短縮につながります。
製品からのモデリング、リバースエンジニアリングサービスも実施しておりますので、伊福精密にお気軽にお問い合わせ下さい。
3D金属プリンター事業のビジネスターゲット
これまで、試作やモックアップへの活用が多かった3Dプリンター。しかし現在、デジタルデータから直接製品を生産する工法の導入が進み、3Dプリンターが活躍する領域は、ますます広がりを見せています。そのような中、特に注目を集めているのが、3Dプリンターにより金属部品を直接製造するDMP(ダイレクト・メタル・プリンティング)。高性能かつ現場でのオペレーションもスムーズな「金属粉末焼結3Dプリンター」が登場したことにより、従来の切削や成形ではできなかった構造を作れる新しい製造プロセスが普及し始めています。
しかも、航空宇宙産業や自動車産業、医療といった高いレベルの品質が求められる分野で、一早く3D金属プリンターの導入が進んでいます。
3D金属プリンターで使用可能な素材一覧
航空宇宙 | エネルギー | ツーリング | 自動車 | タイヤ | デンタル | 医療 | パッケージ | 時計宝飾 | ||
材料 | エアフォイル タービン |
バルブ 熱交換器 |
金型 治具 工具 |
機械部品 | 金型 サイプ |
クラウン ブリッジ 補綴物 |
義肢 インプラント 外科ツール |
フォーミング ブロー成形 射出成形 金型 |
ハウジング | |
鋼材 | マレージング鋼 | ○ | ○ | ○ | ○ | |||||
17-4PH(SUS630相当) | ○ | ○ | ○ | ○ | ○ | ○ | ||||
ニッケル合金 | インコネル718 | ○ | ○ | ○ | ||||||
非鉄合金 | コバルトクロム | ○ | ○ | ○ | ○ | |||||
64チタン | ○ | ○ | ○ | ○ | ○ | |||||
アルミ合金(AISi12) | ○ | ○ | ○ | ○ | ○ |
伊福精密のビジネスモデル
製造業ものづくりの世界が現在、大きく変わろうとしている中、伊福精密は、お客様のものづくりにさらなる価値を提供するための自社技術、3D造形技術の研究開発を推進してまいります。世界市場の動向も常に見ながら、日本国内でのニーズを見極めるとともに、IoTやインターネットデジタル技術を活用したものづくりの在り方を探り、新デジタルものづくり時代に適合したソリューションの開発も進めてまいります。お客様のご要望や用途をヒアリングし、3D金属造形(AM)が適しているのか、従来の機械切削加工(CNC)が適しているのかを見極め、ご提案させていただきます。
“伊福精密が目指すデジタルファクトリ-”&“金型レスものづくり”
伊福精密では、3D造形データや3次元測定結果、従来の切削機械の切削加工データや図面データ等を全て、自社サーバーで一元管理できるインフラシステムを構築してまいります。全ての機械設備やデジタル機器がインターネットで繋がることで、IOTものづくり体制を構築してまいります。
3D金属プリンターについて
3D金属プリンター(AM:Material Addictive Manufacturing)を使用して金属部品を製造する方法は様々ですが、代表的な方法として粉末積層造形方式(パウダーベット方式)と指向性エネルギー堆積(メタルデポジション方式)があります。
パウダーベッド方式では、マルエージング鋼、ステンレス、インコネル、チタン、アルミニウム、コバルトクロムモリブデンなどの材質が使用可能で、メタルデポジション方式では工具鋼や銅なども出来ると言われています。一般的に細かな再現性を求めるならパウダーベッド方式。早さと大きさを求めるならばメタルデポジション方式を採用します。
3D金属プリンターがあれば誰でも簡単に何でも作れると思われがちですが、その範囲は狭く、造形ルールに当てはまらなければ造形不可となる場合があります。また、3D金属プリンターでの量産は不可能なため、少量多品種、または一品一様生産に用いられ、その多くは試作開発品が占めます。現在、3次元水管を配置した金型への応用などにも用いられ、成形サイクルタイムの向上や品質向上の為の新たな工法としても注目を集めています。
3D金属プリンターの製造方法の分類
加工技術のタイプ | 加工方法 | 技術の例 | 素材 |
---|---|---|---|
液槽光重合法 (Vat Photopolymerisation) |
液槽に入れたフォトポリマー(光硬化性樹脂)を光感受重合によって固めていく | ・光造形法(SLA) ・デジタル光加工法(DLP) |
・ポリマー ・セラミックス |
材料噴射法 (Material Jetting) |
液状の材料のしずくを噴射して固めていく | 3Dインクジェットプリンティング | ・ポリマー ・複合材料 |
結合剤噴射法 (Binder Jetting) |
液状の結合材を粉末材料に噴射して固めていく | 3Dインクジェットプリンティング | ・金属 ・ポリマー ・セラミックス |
材料押し出し法 (Material Extrusion) |
材料をノズルまたは穴から押し出す | 熱溶解積層法(FDM) | ポリマー |
粉末床溶解結合(粉末積層)法 (Powder Bed Fusion) |
平らに敷き詰めた粉末材料を熱エネルギーで溶融結合させる | ・選択的レーザー焼結法(SLS) ・選択的レーザー溶融法(SLM) ・電子ビーム溶融法(EBM) ・ダイレクトメタルレーザー焼結(DMLS) |
・金属 ・ポリマー ・複合材料 ・セラミックス |
シート積層法 (Sheet Lamination) |
断面形状に切ったシートを貼り合わせていく | 超音波圧密法(UC) | ・ハイブリッド ・金属 ・セラミックス |
指向エネルギー堆積法 (Directed Energy Deposition) |
材料を堆積させつつ熱エネルギーで 溶融結合させる |
レーザー金属堆積法(LMD) | ・金属 ・ハイブリッド金属 |
パウダーベッド方式とメタルデポジション方式の比較
二つの技術の間で製造方法を検討するときは一般的には製造コスト製造品質がトレードオフの関係になります。
メタルデポジション方式の方がコスト的には10分の1程度で収まりますが、造形品質は寸法
の縮小や複雑デザインの造形は難しくなります。
伊福精密では大きな部品にも対応は可能なパウダーベッド方式の設備を使用しております。
パウダーベッド方式 | メタルデポジション方式 | |
---|---|---|
メリット | ・高い精度 ・高い追加工の加工性 |
・低コスト ・大型部品の製作可 |
デメリット | ・高コスト ・最大加工サイズが小さい |
・デザインに限界あり ・限られた加工精度 |
寸法公差 | ±0.1㎜ | ±0.2㎜ |
最大加工寸法 | 230㎜ × 230㎜ × 230㎜ | 380㎜ × 360㎜ × 740㎜ |
パウダーベッド方式について
パウダーベッド方式による加工
パウダーベッド造形技術は造形を行う為にパーツをスライスデーターを元に各スライス層に大きな熱源でエネルギーを使用して金属化させ積み上げていく事でパーツを製作する技術です。
従来の切削加工の様に粉末ベッド方式の3D金属プリンターでは金型は使用しないため、部品単位に関する初期費用の低減が可能です。
従来の切削加工とは異なり部品をスライスしたデーターにより各スライス層を積み上げて行う加工方式ですので素材(ブランクの意味)は金属粉末の準備のみです。これが積み上げ(添加型)生産方式:アディティブマニュファクチャー(AM)と言われる所以です。この方式では切削加工では不可能な形状や構造を持つ部品の製造が可能です。
トポロジー設計(最適重量・最適構造設計)が可能となり航空機産業や宇宙開発産業に向けて大きなアドバンテージがあります。また各個人向けの量部品(個別設計部品・機材)にて医療分野にも利点は多いです。使用する熱源により4つのタイプに分類されます。
- 選択的レーザー焼結法(SLS)
- SLSは高出力C02レーザーを使用して粉末材料を小片に融合し、3次元部品を作成します。レーザーは、粉体ベッドの表面でX-Y方向の断面をスキャンして、粉末材料を選択的に融合します。モデルは、供給される3D CADデータから、一度に1レイヤを積層します。SLSは、実使用環境で試験するための、非常に耐久性が高い部品を製造する機能を備えます。
- 選択的レーザー融解法 (SLM)
- レーザー光線にて粉末の金属を完全溶解させて固体化します。
ある一定の融解温度の素材のみ使用できます。このためにSLM技術はチタン等の単一元素金属の部品を作成するのに使用されます。 - 電子ビーム融解法 (EBM)
- 上記のレーザーではなく、高エネルギー電子ビームを使用して金属粉末粒子間の融合を行います。
上記の2技術と比較するとよりエネルギー密度が高い為に一般的に非常に造形速度は速いですが薄い立ち壁や複雑形状には不向きです。また、小さな部品も得意ではないです。 - ダイレクトメタルレーザー焼結法(DMLS)
- レーザー光線を利用して金属粉末を分子レベルで焼結させます。
SLS方式の基本構造と造形モデル
SLSは、実使用環境で試験するための、非常に耐久性が高い部品を製造する機能を備えます。
・非常に複雑な形状を生成
・高耐久性、耐熱性、耐化学薬品性アプリケーション
・厳しい用途の耐衝撃性部品
・スナップ フィットや一体ヒンジに最適
・少量生産ソリューション
・時間とコストに大きなメリット
・大型積層プラットフォームも使用可能
標準解像度の公差
X/Y 平面: 最初の1インチは +/- 0.005 インチ、それ以降は1インチごとに +/- 0.005インチ
Z 平面 : 最初の1インチは +/- 0.010 インチ、それ以降は1インチごとに +/- 0.005インチ
SLSは、少量から中量の最終用途部品、エンクロージャ、スナップフィット部品、自動車用コンポーネント、薄肉ダクトなどに好適な、耐衝撃性のエンジニアリング プラスチックから部品を作成します。 SLSは、従来の製造法では多くの組立てを必要とする、少量生産部品に複雑な形状を可能にします。
基本情報
寸法公差 | ±0.100㎜ |
積上造形部 | ±0.025㎜ – 0.150㎜ |
空中造形部 | ±0.100㎜ – 0.150㎜ |
最小壁薄さ | ~0.016’’ (0.4㎜) |
最大造形サイズ | ~ 230㎜ × 230㎜ × 230㎜ |
使用可能な素材
アルミニュウム | 重量あたりの引張り強度が高い |
ステンレス | 高い耐久性と優れた疲労強度あり |
チタン | 非常に強い引張り強度、コストは高い |
インコネル | 高温耐食性に優れる、切削性は非常に悪い |
※素材は完成品の重量の15%程度を付加した重量が素材重量となり、SLS方式の専用の粉末金属が必要となります
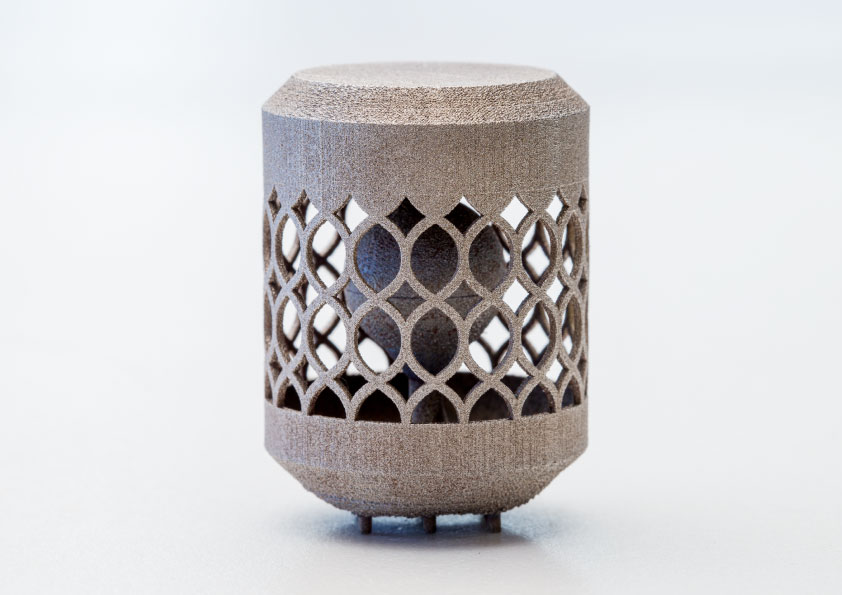
内部に別構造を持つ一体造形品のサンプル。鳥かごの中の球体
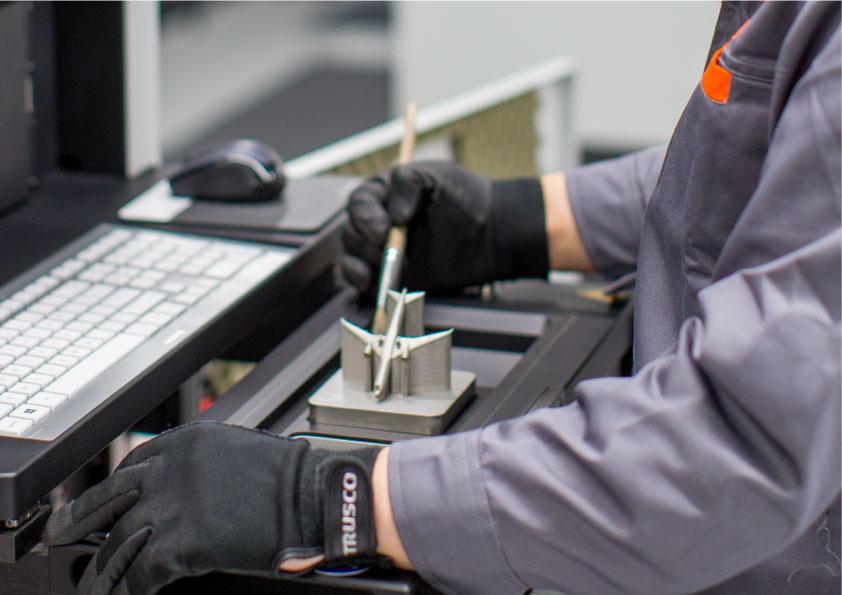
造形後の取出し状況
表面仕上げの種類
造形仕上げ | 造形用のサポート部分を取り除き、表面を滑らかにします。 表面粗さ ~8.75 RA µm. |
ショット仕上げ | 軽い質感のマット仕上になります。 ガラスやその他の研磨剤を圧縮空気と共に吹付けてパーツの表面を改善します。 仕上り表面は1.6 Ra µm程度になります。 |
ポリッシュ研磨仕上げ | 腐食に対する耐性を向上させて摩擦係数を低減させます。 ガスタービンの様な要求の厳しい表面仕上に適応します。 仕上り表面は0.8 Ra µm程度になります。 |
メッキ仕上げ | 金属メッキは様々な部品特性を改善するのに有効です。 腐食、耐熱、強度、導電性等も改善されます。 |
※その他の表面処理もご相談に応じて対応させていただきます。
金属の特性
金属・鋼 | 密度(g/c㎥) | 硬さ(Hv) | 引張強さ(N/m㎡) |
---|---|---|---|
SUS304 | 7.93 | 150 | 600 |
SUS316 | 7.98 | 145 | 590 |
SUS420 J2 | 7.78 | 247 | 540以上 |
SUS630 | 7.78 | 345 | 725 |
17-4PH | 7.75 | 331 | 896 |
6-4チタン | 4.43 | 310 | 980 |
マレージング鋼 | 8.02 | 320 | 985 |
ACD3アルミ | 2.63 | – | 320 |
5052アルミ | 2.68 | – | 195 |
伊福精密の3D金属造形設備
リバースエンジニアリング
ものづくりにおけるリバースエンジニアリングとは、製品の先行イメージとして作られたクレイモデルや、既に現物がある製品などの形状データを測定(スキャニング)し、それをもとにCADデータを作成することです。3次元測定器や3次元スキャナで製品または現物を測定し、忠実に再現します。様々な工法や素材で製作が可能です。
3Dデータはないが実物があるという場合にご利用されています。摩耗した金型修復や、3Dモデル製作なども低コストおよび短期間で対応が可能です。
また、3D金属プリンターで造形した物とCADデータの整合性を見る検査(比較検査)としても利用しております。非接触式なので複雑な形状検査などでも利用されます。
弊社では3D金属プリンターを保有しているため、スキャンしたデータから3Dプリントをする事も可能なので一貫したサービスを提供する事が出来ます。
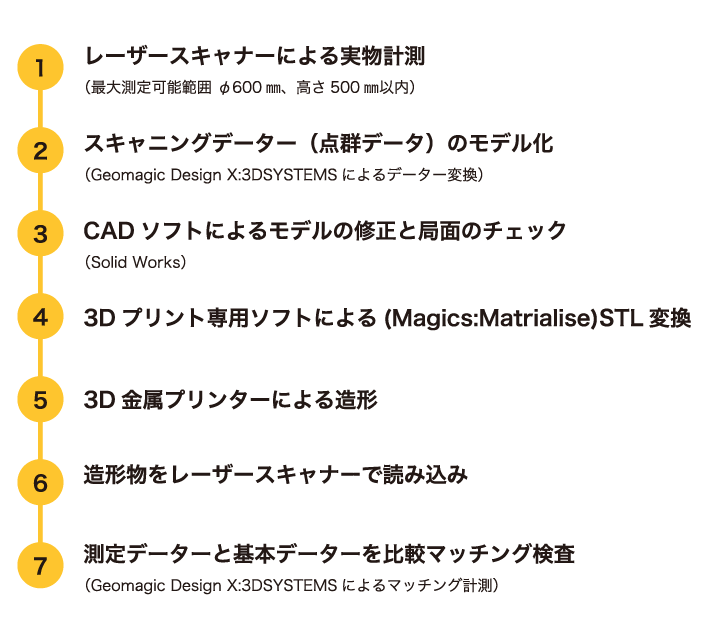